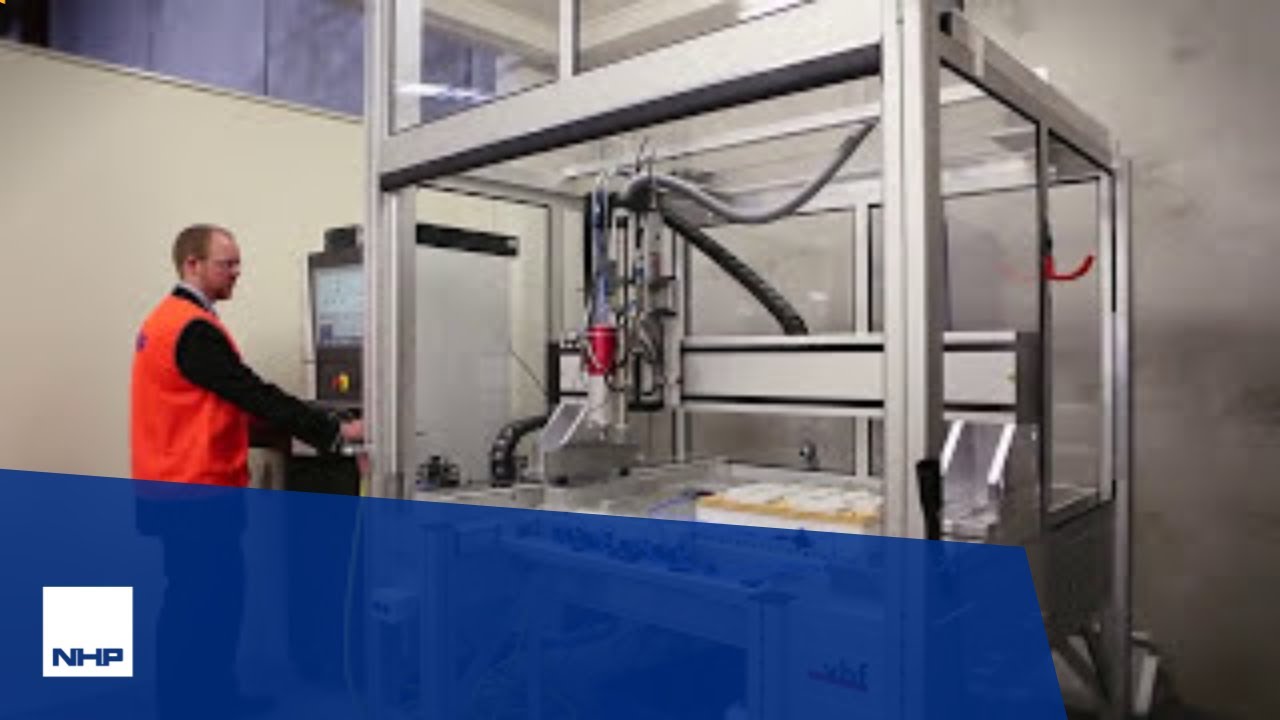
To satisfy the fundamental requirements of CNC machining, a variety of machine shop operations need to be done, including turning, milling, facing, and more. Conventional machining procedures are excellent for high stock removal and excellent surface quality, using two or two procedures. The roughing operation is utilized in a short time to generate a component geometry near to the finalized product shape, and finishing operation is conducted after roughing to accomplish final geometry and other features.
Rough machining may identify different blank faults, such as sand hole, air hole, inadequate machining allowance, etc., convenient for quick repair or scrapping, so as not to waste processing time and expense. Rough machining is prepared before mechanical finishing and finishing may preserve the surface from wear.
What are NPT Thread Dimensions?
Roughing may perform quick feed and the fault may be repaired by the subsequent finishing to assure quality.
Rough operation in machining is largely used to quickly and roughly shape the workpiece to the required shape, making future processing more easy and efficient. The objective of rough machining is to swiftly remove the blank allowance, generally using big feed rate and cutting depth to remove as many chips as possible in a short period. Rough machined goods generally obtain poor precision, rough surface, and high productivity. The roughing procedure is typically semi-finishing and finishing. After hot work, the workpiece's residual stress is significant, separating rough and finish machining, aging may be managed to reduce residual stress, and finishing may be done to remove deformation after cooling.
Difference between tough and finish
Commonly used NPT thread sizes (including 1/8, 1/4, 3/8, 1/2, 3/4, 1, 1+1/4, 1+1/2, 2, 2+1/2, 3, 4, 5 and 6 inches) may be found on most U.S. pipes. Thread sizes lower than 1/8" and greater than 6" are sometimes employed for special uses. In the NPT thread size chart, the pipe size does not correlate to any physical measurements, ABS Uses is utilized as a trade size. When identifying or defining a thread size, threads-per-inch and the thread's external diameter are essential since more than one size has the same TPI. A pipe or fitting OD must be measured and matched to a thread size chart for identification.
Rough Machining advantages
When the melt flows in the mold cavity, the solidification layer is attached to one end of the molecular chain near the solidification layer and the neighboring molecular chain stretches in the flow direction. Because the flow resistance of the melt near the cavity wall is the highest and the flow rate is the lowest, while the flow resistance in the center of the cavity is the lowest and the flow rate is the biggest, forming the velocity gradient in the direction of flow. Therefore, when the injection rate is low, the injection pressure is high or the thickness of the product is thin, the melting force near the cavity wall is the highest and the degree of orientation is the biggest, The polymer reveals internal stress when stretched in flow, resulting in fluorescent lines appearing on the product surface.
The benefits of rough and final machining equipment may be fully used. Roughing equipment has high power, high efficiency and strong stiffness, and high accuracy and low error finishing equipment.
Rough vs Finish
In the melt filling process, the fresh melt flow is continually forced out of the inner layer, driving the front wave to stagnate and move. The front wave edge is continually extended. The later melt pressure increases and the front wave is flattened due to flow resistance, resulting in stagnant buildup and product surface waviness. Especially for high injection rate, low injection pressure or inappropriate mold construction, melt flow in and out, and PP crystallization in and out, the product's surface crystallinity is more likely to be inconsistent, generating wavy lines on the product's surface.