A beginners guide to creating your own 3D CAD drawings
Throughout the history of computer-aided design (CAD), new variations of project files have evolved. Autodesk's AutoCAD, which implemented the DWG file format, was one of the first viable PC alternatives to CAD. This was Autodesk's patented method of storing 2D and 3D images created in AutoCAD, along with all associated metadata.To get more news about drawing cad, you can visit shine news official website.
As the industry evolved, DWG became the mainstream 3D CAD file format. However, as CAD systems evolved and expanded their capabilities, they required innovative ways to store new technologies while maintaining novel code and remaining graphics-focused. To meet this demand, a number of new 3D CAD file formats have been created.
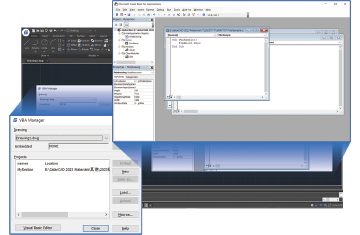
3D CAD file creation tools
Engineers and designers use 3D modelling, or CAD, to create realistic virtual models of parts and assemblies. These models can then be 3D printed, CNC machined or used to run complex simulations. A wide range of parameters, such as strength or temperature resistance, can be simulated before physical models are developed, enabling a much faster and more cost-effective workflow.
Solid Modelling
Solid modelling produces solid 3D models that behave like physical objects, with a logical workflow that resembles the processes that would be used to manufacture the part. Extrusion, drilling and threading are examples of these activities. Solid models can be overlapped, combined and removed to create the desired part.
Another advantage of solid modelling is that it is usually parametric, which means that adjustments or parameters are saved at each stage of the modelling process and can be edited at any time during the design process. This is very useful as it allows you to easily change the characteristics of the model without having to rebuild the component from scratch.
Assembly modelling is also an important stage in solid modelling. It allows individual parts to be assembled into complex models. Standard parts, such as fasteners or bearings, can be inserted into assemblies downloaded directly from the manufacturer. Motion elements can also be added to assemblies, allowing thorough motion analysis to determine the overall performance of the design.
Surface Modelling
Surface modelling is typically used for the more aesthetic features of a product. This type of CAD software makes it much easier to create organic and free-form geometry. Many of the limitations that exist in solid modelling do not exist in surface modelling, at the cost of sometimes less accuracy.
Surface modelling, as the name suggests, consists mainly of the surfaces of the part, with no solid interior. The segment can then be filled and used for 3D printing until it has enough faces to close it. Because surface modelling is typically not parametric, it can be difficult to go back and make adjustments during design.
This type of modelling software has advantages and disadvantages that must be considered depending on the type of design being created. To combine the advantages of solid and surface modelling, it is often necessary to use both.
Sculpting
Sculpting, also known as organic modelling, is primarily used to create free-form surfaces with intricate details such as characters, jewellery or organic forms found in nature such as trees or rock formations.
Classic sculpting software packages such as Pixologic's ZBrush or Autodesk's Mudbox were created with this in mind. They allow digital sculptors to start with a simulation ball of clay and control their object with brushes that represent classic sculpting tools such as a small rake or thumbs to move, add or remove material from their object using a pressure-sensitive drawing tablet or monitor.